The interest in lean construction appears to have declined in recent years. The Google Trend graph below shows that searches for lean construction have fallen to a fraction of the number of searches 10 years ago. No doubt there are many reasons for this. In part Lean has lost its newness. It was explicit in Egan (1998) and lean thinking was central to the year on year savings that Egan called for. At that time it seemed that lean through Partnering was the panacea that was going to transform the industry from an adversarial past to brave new collaborative world.
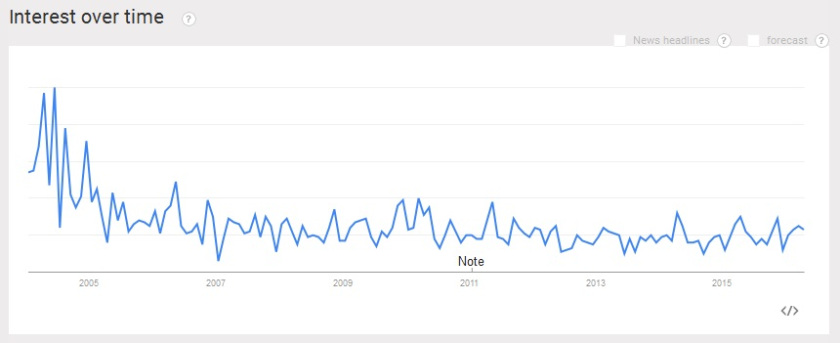
Since Egan there have been a series of government reports including Accelerating Change (intended to reinvigorate the drive towards Egan’s principles); Never Waste A Good Crisis (lean less explicit but lean principles still strong eg ‘This means understanding how value is created over the whole life cycle of an asset, rather than simply looking at the building cost, which is only a part of the total equation. It is about how the relatively small up-front costs of design and construction can have such huge consequences for future users, whether expressed as business or social outcomes, as well as for the environment. ‘, to the most recent of these the ‘ UK Government Construction Strategy’ (2011) which mentions lean only in terms of a ‘lean procurement strategy’ (for lean read efficient) and ‘Construction 2025’ (2013) which does not mention lean at all.
Apparently, there is no need to fear though! Construction 2025 contains four new targets:
- A 33% reduction in both the initial cost of construction and the whole life cost of assets.
- A 50% reduction in the overall time from inception to completion for new build and refurbished assets.
- A 50% reduction in greenhouse gas emissions in the built environment.
- A 50% reduction in the trade gap between total exports and total imports for construction products and materials.
While it is not certain exactly how these savings will be achieved it is clear that the major driver for these will be Building Information Modelling. The Government’s Industrial Strategy for BIM estimated that BIM would go a long way to helping the government meet its target of a reduction of 15-20% in capital delivery costs by 2015. This in turn is based on an ‘Investor’s Report’ (2008) that details potential savings at each stage of the construction lifecycle. So once again we have big efficiency savings to be made and the means to achieve these. In 1998 partnering was going to achieve the targets and now BIM is going to do the same.
Before I go further I should state clearly that I was a big supporter of Egan. I also believe strongly in the potential benefits of partnering and BIM. What worries me is this: I can’t see in any of these reports a theoretical basis as to why the savings called for might be expected to be achieved. The use of the word theory might seem to many to be an abstract concept – a word used by academics, rather than practical people with real jobs to do. But, as Van de Ven says, ‘there is nothing so practical as a good theory’. A good theory means that we can understand the simplest and most basic questions of Who, What, Where, How, When and most importantly Why? So, to put it more simply the reports are strong on Who, What, Where and to some degree How. But for people to successfully put ideas into practice they need to understand Why.
It is at this point that I want to go back to Lean Construction. Sometimes people say ‘lean doesn’t work in practice’ and at other times people say ‘lean is just common sense’. To me lean works because it is based on strong theoretical principles. It is true that these principles are ‘common sense’, but as we all know common sense is rare. As to whether or not ‘it works in practice’, I would say it won’t work unless the theoretical principles are understood. In other words, unless we understand Why. So what are these theoretical principles that need to be understood? In my opinion these principles are captured best by my friend and (ex) colleague Professor Lauri Koskela. Lauri summarised lean thinking for construction with his TFV model. This model tells us to consider three things:
- Transformation – While it is important to try to improve the efficiency of individual process, unless F & V are considered first this may be counter-productive resulting in sub-optimisation.
- Flow – Processes should be aligned to eliminate wasteful activities and to deliver V to the customer
- Value – The most important point is that customer value must be understood and maximized where possible. It is this that should drive the F and then the T
To summarize: Projects can only truly be successful if all parties work towards delivering Value from the customer perspective. Once this is understood processes should be aligned to meet this aim and non-value adding activities eliminated. Once this is done then it is worthwhile working to improve individual processes or transformations. These are the theoretical (or common sense) principles on which lean is built and are often forgotten in practice.
If we expect to make the savings called for in Construction 2025, or through the use of BIM, it is important that these principles are remembered. In particular, it is important that we start with V. In my opinion this is the aspect that is most frequently forgotten, and yet is the most important aspect. Concentrating on V, i.e. maximizing and delivering value to the customer would force us to consider how we might change things from making ‘business as usual’ incrementally more efficient, towards delivering value to the client. By far the most important consideration for the client is that the building delivers value to its business. This tells us that strategy, briefing and design, when helping to meet the needs of the client, are value adding activities. So the consideration of these stages of the process should not be how we can increase the efficiency the stages (as is done in the Investment Report) but how we can use this time to maximum advantage. In fact, as this time is value adding it might even be better to extend the time so as to maximize value. Once we can understand this, then we can look at how we might arrange processes to flow in order to meet clients’ needs. In my opinion, if we started from this viewpoint the processes and the roles associated with them would change radically. As it stands, although there are some notable exceptions, the focus is on how we maximize the efficiencies of existing processes. In my next post I will discuss further what this transformation might look like.